本文主要是介绍最长连续子序列偏移_在新的模压成型工艺中结合热塑性连续带材与DLFT(第一部分)...,希望对大家解决编程问题提供一定的参考价值,需要的开发者们随着小编来一起学习吧!
一项由德国联邦教育与研究部门监督、名为“为电动汽车的应用而系统地集成多材料体系的轻量化设计”(简称“SMiLE”)的为期多年的公共资助项目,通过组合复合材料与有色金属,降低了电池电动汽车整个白车身结构的重量和成本。
其中,后地板模块的设计,采用了两种类型的热塑性复合材料以及金属型材和嵌件。
为实现该承重地板的快速、低成本生产,一种新的一步法模压成型子工艺被开发出来,同时还采用了一种用于快速加热和固结热塑性带材的新技术。
UD带+D-LFT
一个运行多年的德国研究项目,通过最有效地使用复合材料和有色金属材料,来寻求降低一款电池电动汽车白车身结构重量的方法。该项目的一部分是,研究生产复合材料后承重地板的方法,即在UD带层压板中,有选择性地采用D-LFT来包覆成型肋、金属嵌件和铝型材。为了生产该部件,一种新的D-LFT/模压成型子工艺以及一副非常复杂的模具被开发出来。此外,早期开发的一种方法,可将热塑性复合材料的带叠层快速加热并固结成一种用于生产这种新型示范部件的订制拼接的层压板(图片来自弗劳恩霍夫ICT)
这种混合的复合材料后承重地板,采用了热塑性的单向(UD)带和直接长纤维热塑性(D-LFT)复合材料:
►热塑性的带材为薄的轻质结构提供了高刚性和高强度,使其能够在碰撞中承受高屈曲载荷;
►D-LFT则提供了成型复杂形状、实现功能集成/部件整合的能力,而且能够嵌入成型金属附件。
该部件采用了Ultramid B3K PA6 D-LFT(含40%重量百分比的玻纤增强材料)和8层Ultratape B3WG12 PA6带材(含60%重量百分比的玻璃纤维),这两种材料均由巴斯夫提供。
虽然可以对D-LFT进行注塑成型或模压成型,对带叠层进行包覆注塑成型,但这两种材料通常是被模压成型的——这是一种耳熟能详的汽车生产工艺,在本地和全球都拥有足够的装机产能,可支持SMiLE项目实现“每天生产300辆汽车”的目标。
采用下述两种方法之一,就可以在同一个部件中组合UD带与D-LFT:
►一种方法是,有选择性地将UD带添加到D-LFT主结构中需要更好力学性能的承载路径上,这被称作“订制D-LFT”, 也可以采用连续纤维粗纱来代替UD带,或者与UD带结合使用。
►第二种方法是,在部件的对面覆盖UD带和D-LFT。
采用第一种技术,可流动的D-LFT易在包覆成型过程中推动薄的UD带发生位置偏移,因此,需要在模内使用夹子或其他硬件来保持UD带固定不动。虽然在D-LFT 主结构中有选择地使用UD带的成本较低,但这样的部件,却不像那些将更高比例的UD带用于D-LFT的部件那样强或轻。
采用第二种技术,在部件的另一面应用UD带和D-LFT, 可以通过D-LFT实现更好的功能集成/部件整合,通过UD带实现更高的刚度和强度,但由此而获得的结构仍然相对较重,而且不能达到它所能达到的强度与刚度。
基于汽车承重地板关键的安全性要求,以及 SMiLE的研究人员希望使用完全由热塑性复合材料制成的后承重地板(不只是在传统的全金属承重地板或新的混合-复合材料承重地板的轴侧安装金属型材)来吸收碰撞能量,使后承重地板尽可能坚固是非常重要的。
为同时降低重量和成本以实现项目目标,研究人员们想要在避免发生碰撞屈曲的同时让承重地板更薄,还想在关键位置添加功能(比如用于第二排座椅安全带的连接点),为此,他们开发了一种新的 D-LFT/模压成型子工艺:承重地板主要采用热塑性带材(在成型前预固结成一个层压板),D-LFT只是有选择地应用在需要加强肋和复杂几何结构的地方,因为这些单靠带材层压板是不可能被成型出来的。
该团队还决定尝试在一个单独的步骤中、在模压机内生产1.3m×1.3m的后承重地板。为了实现所有这些目标,该团队需要综合采用有趣而创新的模具以及连续的成型工艺。
局部高级订制的LFT
该后承重地板的最终设计是一种近净形状的薄壳结构,通过将UD带预固结成一个层压板而被生产出来。
沿部件纵轴含有大的波纹形状,能够在确保高强度的同时降低重量并减小厚度。但研究人员们知道,在大型层压板中成型出这些波纹是困难的。
为了确保良好的悬垂效果,在模具设计中应用了仿真技术,以验证波纹成型的可重复性(50mm高,115mm宽)并最大程度地减少褶皱。
如果出现了差错以及波纹没有正确成型,该层压板可能会起皱或偏离平面,与D-LFT的粘接强度就会很差。
虚拟原型预测的最佳成型顺序是,从内部/中心向外朝向侧面,类似于通常的手工铺层做法。只有这样,才能在一个利用工具(滑块)运行的成型步骤中(层压板的预成型不是在主压机外部完成的),完成连续的成型过程。
滑块在非常复杂的注塑成型模具中是常见的。虽然滑块在模压成型中并非闻所未闻,但却不太常见,而且在使用时复杂程度往往要低得多。
研究人员们设计了拥有6个可置换型腔的模具(采用4个滑块)来成型层压板中的波纹和其他结构,而不仅仅是在D-LFT中包覆成型它们,否则会大大增加部件的重量和厚度。
对层压板/D-LFT肋连接处的界面强度进行的前期研究表明,如果在包覆成型之前,层压板至少保持130℃的温度(低于PA6基体材料的熔点),D-LFT在280 ℃的温度下(高于PA6的熔点)被放入模具中,就可以获得优良的粘接强度。
为防止在放上D-LFT坯料之前,层压板在模具上过快冷却,研究人员将它放到模具型腔侧完全伸出的顶出杆上。
当放上两个D-LFT坯料时,顶出杆下降,模具开始闭合。接着,4个滑块(其中3个利用机器的液压系统运行,第四个通过弹簧操作)依次展开,对层压板进行成型,包括其深波纹形状。
一旦压机完全闭合,D-LFT肋结构(在复杂的X形格子中)即被成型出来。
研究人员们将其命名为“局部高级订制LFT的顺序成型技术”。
另一个与传统模压模具设计不同的是,为了针对不可流动的带材层压板(构成结构的主体)有选择地成型可流动的D-LFT坯料,该模具仅在D-LFT流向部件边缘的部分才拥有剪切边。
值得一提的是,弗劳恩霍夫化学技术研究院(简称“弗劳恩霍夫ICT”)曾在更大的SMiLE项目中领导了前、后承重地板的开发,还与其他项目合作伙伴一起,协助开发了“局部高级订制LFT的顺序成型工艺”。
敬请关注后续报道:
辐射诱导的真空固结技术与最后的工序
点击标题查看往期文章精选
骨架设计实现更具竞争力的复合材料汽车结构
VOGEL-PT要闻播报
零塑胶天然材料的注塑工艺
JetPreg:轻量化的解决方案
TEMIone:面向单台注塑机的全面的MES解决方案
科莱恩推出用于聚酯包装的新的CESA® ProTect品牌脱氧添加剂
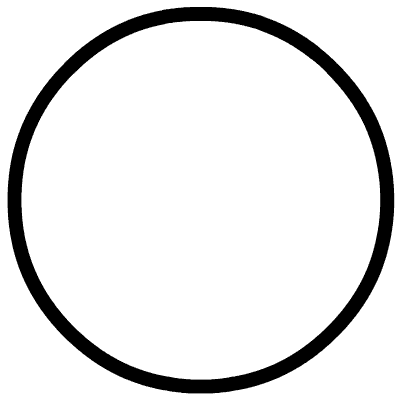
这篇关于最长连续子序列偏移_在新的模压成型工艺中结合热塑性连续带材与DLFT(第一部分)...的文章就介绍到这儿,希望我们推荐的文章对编程师们有所帮助!